قسمت 1: دنده و قطعات سیستم تعلیق خودرو
1. فرآیند ماشینکاری دنده
با توجه به الزامات ساختاری مختلف، فرآیند اصلی تکنولوژیکی پردازش قطعات دنده عبارت است از فورج → نرمال کردن → ماشینکاری تکمیل → شکل دهی چرخ دنده → پخ → حباب → تراشیدن → (جوشکاری) → عملیات حرارتی → سنگ زنی → پیرایش مش.
دندان ها معمولاً بعد از گرما ماشین کاری نمی شوند، به جز دندان های اصلی و فرعی یا قطعاتی که مشتری برای تراشیدن دندان ها نیاز دارد.
2. جریان فرآیند شفت
شفت ورودی: شمش آهنگری → عادی سازی → ماشینکاری تکمیلی → نورد دندان → سوراخکاری → شکل دهی دندان → پخ زدن → حباب → تراشیدن → عملیات حرارتی → سنگ زنی → پیرایش مش بندی.
شفت خروجی: شمش آهنگری → عادی → ماشینکاری تکمیل → سنگ زنی و سنگ زنی → اصلاح → عملیات حرارتی → سنگ زنی → تریم جفت.
3. جریان فرآیند خاص
(1) شمش آهنگری
فورج قالب داغ یک فرآیند فورج خالی برای قطعات دنده خودرو است. در گذشته، فورج گرم و بلانک های اکستروژن سرد به طور گسترده مورد استفاده قرار می گرفت. در سال های اخیر، فناوری نورد متقاطع گوه به طور گسترده ای در پردازش شفت ترویج شده است. این فناوری مخصوصاً برای ساختن صفحات برای شفت های پلکانی پیچیده مناسب است. این نه تنها دارای دقت بالا و مزایای پس از پردازش کوچک است، بلکه راندمان تولید بالایی نیز دارد.
(2) عادی سازی
هدف از این فرآیند به دست آوردن سختی مناسب برای برش دنده بعدی و آماده سازی ساختار برای عملیات حرارتی نهایی است تا به طور موثر تغییر شکل عملیات حرارتی را کاهش دهد. نرمال سازی عمومی تا حد زیادی تحت تأثیر پرسنل، تجهیزات و محیط قرار می گیرد و کنترل سرعت خنک کننده و یکنواختی قطعه کار را دشوار می کند و در نتیجه پراکندگی زیادی از سختی و ساختار متالوگرافی ناهموار ایجاد می شود که مستقیماً بر ماشینکاری و عملیات حرارتی نهایی تأثیر می گذارد.
(3) ماشینکاری تکمیل
به منظور برآوردن نیازهای موقعیت یابی پردازش دنده با دقت بالا، از تراش های CNC برای تکمیل قطعات دنده استفاده می شود. ابتدا سوراخ داخلی و وجه انتهایی موقعیت یابی چرخ دنده پردازش می شود و سپس پردازش وجه انتهایی دیگر و قطر بیرونی به طور همزمان تکمیل می شود. این نه تنها الزامات عمودی سوراخ داخلی و موقعیت قرارگیری وجه انتهایی را تضمین می کند، بلکه اطمینان می دهد که پراکندگی اندازه تولید دندان خالی در مقیاس بزرگ کوچک است. بدین ترتیب، دقت دنده خالی بهبود یافته و کیفیت پردازش چرخ دنده های بعدی تضمین می شود.
سه روش اصلی برای قرار دادن و بستن برای پردازش قطعات شفت وجود دارد:
1. تعیین موقعیت با سوراخ مرکزی قطعه کار: در پردازش شفت، هم محوری هر سطح خارجی و وجه انتهایی قطعه و عمودی سطح انتهایی به محور چرخش موارد اصلی موقعیت متقابل آنها است. دقت. اساس طراحی این سطوح به طور کلی هر دو خط مرکزی شفت هستند. اگر از دو سوراخ مرکزی برای موقعیت یابی استفاده شود، با اصل همزمانی مبنا مطابقت دارد.
2. دایره بیرونی و سوراخ مرکزی به عنوان مرجع تعیین موقعیت استفاده می شود (یک گیره و یک بالا): اگرچه دقت مرکز بالا است، سفتی ضعیف است، به خصوص هنگام پردازش قطعات سنگین تر، به اندازه کافی پایدار نیست و برش مقدار نباید خیلی زیاد باشد در حین ماشینکاری خشن، به منظور بهبود صلبیت قطعه، می توان از سطح بیرونی شفت و یک سوراخ مرکزی به عنوان مرجع موقعیت یابی برای پردازش استفاده کرد. این روش موقعیت یابی می تواند یک لحظه برش زیاد را تحمل کند و رایج ترین روش موقعیت یابی برای قطعات شفت است.
3. از دو سطح دایره ای بیرونی به عنوان مرجع تعیین موقعیت استفاده کنید: هنگام ماشینکاری سوراخ داخلی محور توخالی (به عنوان مثال: ماشینکاری سوراخ داخلی مخروطی مورس روی ماشین ابزار)، سوراخ مرکزی نمی تواند به عنوان مرجع تعیین موقعیت استفاده شود. و از دو سطح دایره ای بیرونی شفت می توان به عنوان مرجع تعیین موقعیت استفاده کرد. داده موقعیت یابی هنگامی که قطعه کار دوک ماشین ابزار است، از دو ژورنال پشتیبان (مقطع مونتاژ) اغلب به عنوان مبنا موقعیت یابی استفاده می شود که می تواند از هم محوری سوراخ مخروطی نسبت به ژورنال نگهدارنده اطمینان حاصل کند و خطای ناشی از عدم تراز را برطرف کند. از داده ها
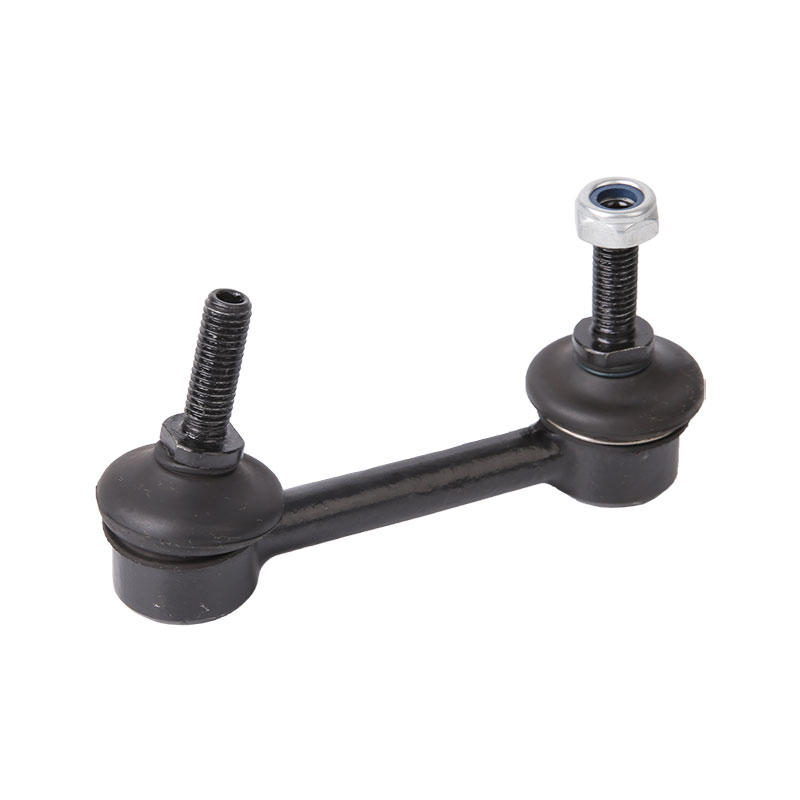
قسمت دوم: قطعات پوسته
1. جریان فرآیند
جریان فرآیند کلی عبارت است از سطح اتصال فرز ← سوراخهای فرآیند ماشینکاری و سوراخهای اتصال ← سوراخهای حفاری خشن ← سوراخهای حفاری ریز و محل سوراخهای پین ← تمیز کردن ← تشخیص تست نشت.
2. روش کنترل
(1) وسایل
فرآیند ماشینکاری محفظه انتقال به عنوان مثالی از "ماشینکاری مرکز ماشینکاری عمودی" در نظر گرفته شده است. فرآیند 10# ماشینکاری مرکز ماشینکاری عمودی 20# فرآیند ماشینکاری مرکز ماشینکاری افقی فرآیند 30#، برای جلوگیری از قطعه کار به سه مجموعه از وسایل مرکز ماشینکاری نیاز است. تغییر شکل بستن نیز باید در نظر گرفته شود، مانند تداخل ابزار، عملکرد انعطاف پذیر، قطعات متعدد و یک گیره، و سوئیچینگ سریع.
(2) جنبه ابزار
در هزینه ساخت قطعات خودرو، هزینه ابزار 3 تا 5 درصد از کل هزینه را تشکیل می دهد. ابزار کامپوزیت با ساختار مدولار دارای ویژگی های دقت بالا، نگهدارنده ابزار قابل استفاده مجدد و موجودی کوچک است و به طور گسترده مورد استفاده قرار می گیرد. این می تواند زمان پردازش را تا حد زیادی کوتاه کند و کارایی کار را بهبود بخشد. بنابراین، زمانی که الزامات دقت بالا نیست و ابزارهای استاندارد می توانند به نتایج پردازش بهتری دست یابند، باید تا حد امکان از ابزارهای استاندارد برای کاهش موجودی و بهبود قابلیت تعویض استفاده کرد. در عین حال، برای قطعات تولید انبوه، استفاده از ابزارهای پیشرفته کامپوزیت غیر استاندارد برای قطعات با نیازهای دقت بالا می تواند دقت ماشینکاری و راندمان تولید را بهبود بخشد.